Enterprise War Room
Clear Visualized Operation Management
NexAIoT uses the self-developed iAT2000 Cloud SCADA System to bridge the gap between OT and IT in the fields of industrial communication, equipment, and heterogeneous data integration. This open-architecture industry 4.0 comprehensive solution was implemented in NEXCOM’s Huaya Factory, and this smart factory became an important milestone for NEXCOM. The establishment shows that we have evolved from an IPC factory to a diversified smart solution group that provides smart manufacturing, smart machinery, and smart monitoring services. The whole world is talking about Industry 4.0, but few can provide practical solutions. Our Intel CPU-based edge computing platform has developed an all-inclusive solution that can centrally manage distributed resources and has implemented the main elements of true Industry 4.0 in our Huaya Smart Factory. We have proved that we can increase the critical KPIs in daily operations by 15% to 25%. We can assist manufacturers in successful digital transformation and achieve the best benefits of asset digitization, equipment networking, and intelligent management and operation.
Features
iAT2000 Cloud SCADA System
- High-performance PC-based Automation System
- A wide-range Integration System
- Edge Server with advanced data and service pre-processing
Enterprise War Room that Masters the Real-time Factory Operation Data
- 9 OT/IT modules that measure key performance indicators (KPI)
- Multiple TV wall combinations with 5-8 LCD screens and 16K digital screen server
- Integrated ERP/MES/SCADA management chart information
Profit-oriented iPDM4.0 Manufacturing Management
- 18 manufacturing process management rules
- Real-time status of work order or order cost
- Efficient problem solving or strategy management module
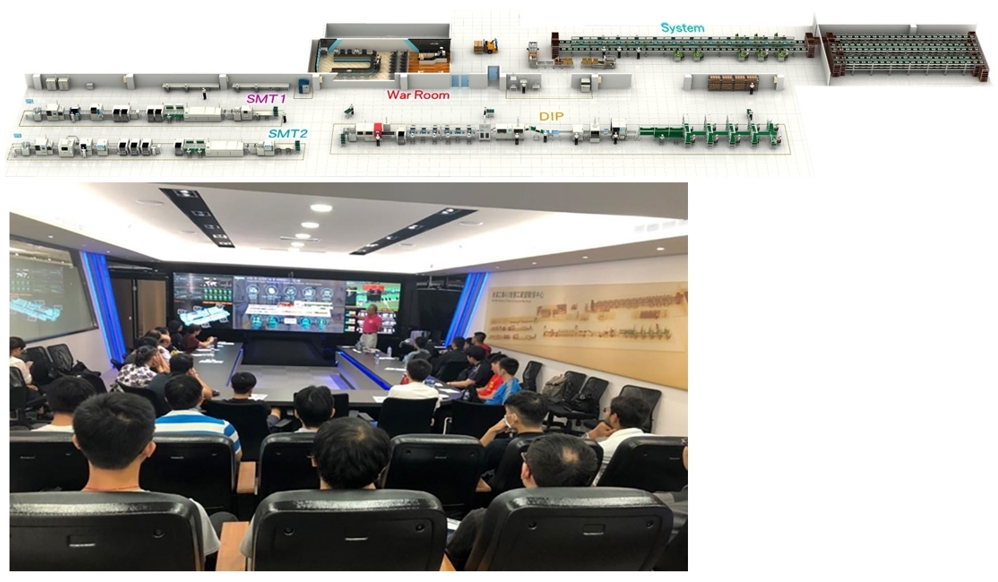
Nexcom Hwaya Factory and Enterprise War Room Information
- Location:Huaya 3rd Rd, Guishan Dist., Taoyuan, Taiwan
- Footprint :8000 m2
- Display:4x2(8)55”(7M Width)LCD TV Wall/9Modules
- Application:3C Produciton Line, 2xSMT; 1xDIP
- Accomodation : 30 seats in Enterprise War Room
9 Modules
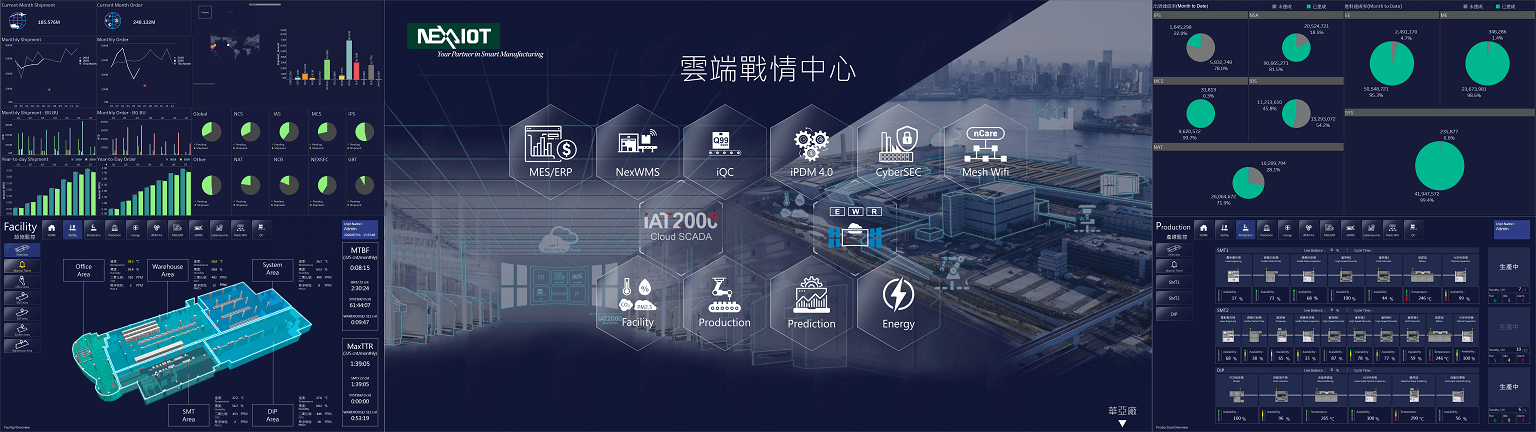
Production
The production machine uses gateway’s smart machine box to collect the SMT and DIP machines’ operation, production, and throwing status. iAT2000 integrates machines of different brands and their protocols and performs big data analysis of the reflow furnace’s temperature and quality. iAT2000 not only carries out real-time machine operation monitoring and production information reading but also dynamically adjusts the machine's process parameters.
Facility
For factory facilities, the iAT2000 system has incorporated the temperature and humidity of the burn-in room, and the temperature, humidity, and PM2.5 of air compressor, nitrogen supply, and factory environment into the plant-wise monitoring system. The system also integrates IP cameras for video monitoring and adopts the latest sensor integration with IoT gateways technology. iAT2000 can directly link to the monitor and issue commands for parameter adjustments when an abnormal status occurs.

Energy
The iAT2000 system performs detailed circuit monitoring for each production machine, air cooled packaged water chiller unit, and lighting power circuit. The monitoring is divided into the peak, half peak, and off-peak periods to analyze the power consumption and make the best deployment of the production line. The water consumption of the chiller unit is monitored and converted into electricity consumption to adjust the number of air handling unit used to optimize air-conditioning power usage.
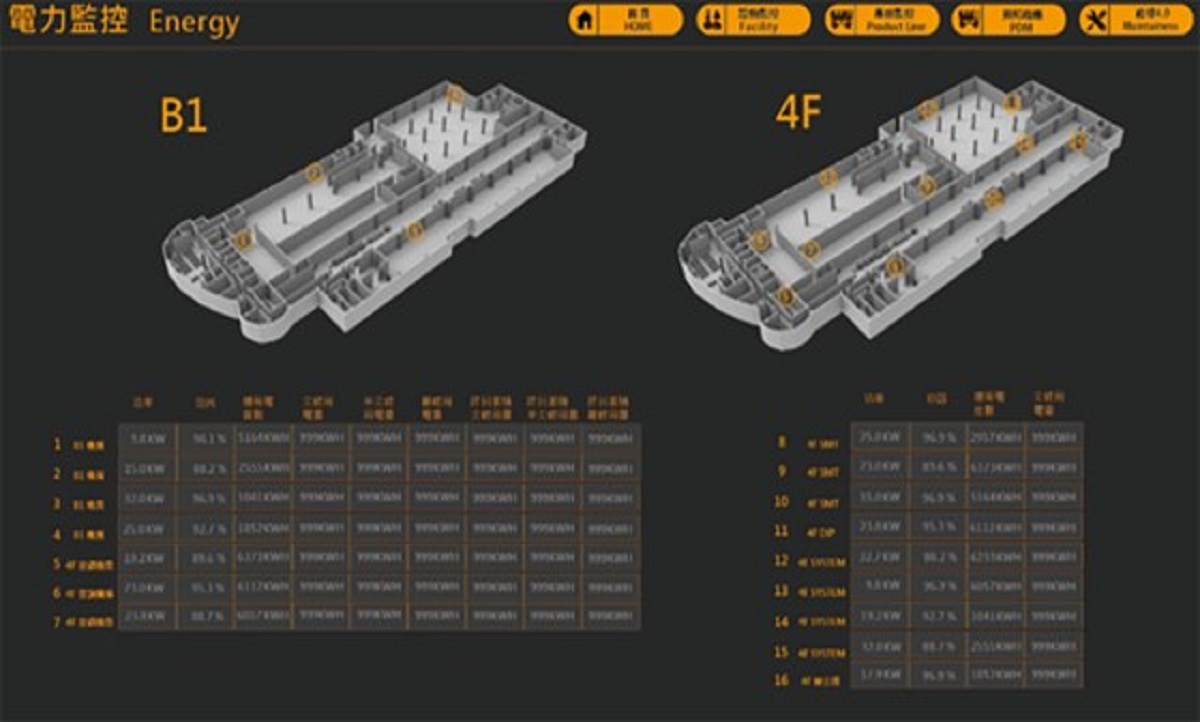
Prediction
iAT2000 forecasts the health diagnosis and energy-saving deployment of major equipment, hoping to achieve zero downtime and repair schedules, and introduces the preventative maintenance expert system developed by NEXCOM. The system targets the tin furnace tin wave control motor of DIP-line, the thermal cycle motor of the SMT reflow furnace, the air compressor motor, and the exhaust motor to perform the vibration spectrum analysis on the bearings and blades of the motors. This method of using machine learning to calculate the motor parts’ life expectancy is a unique and cost-effective solution.
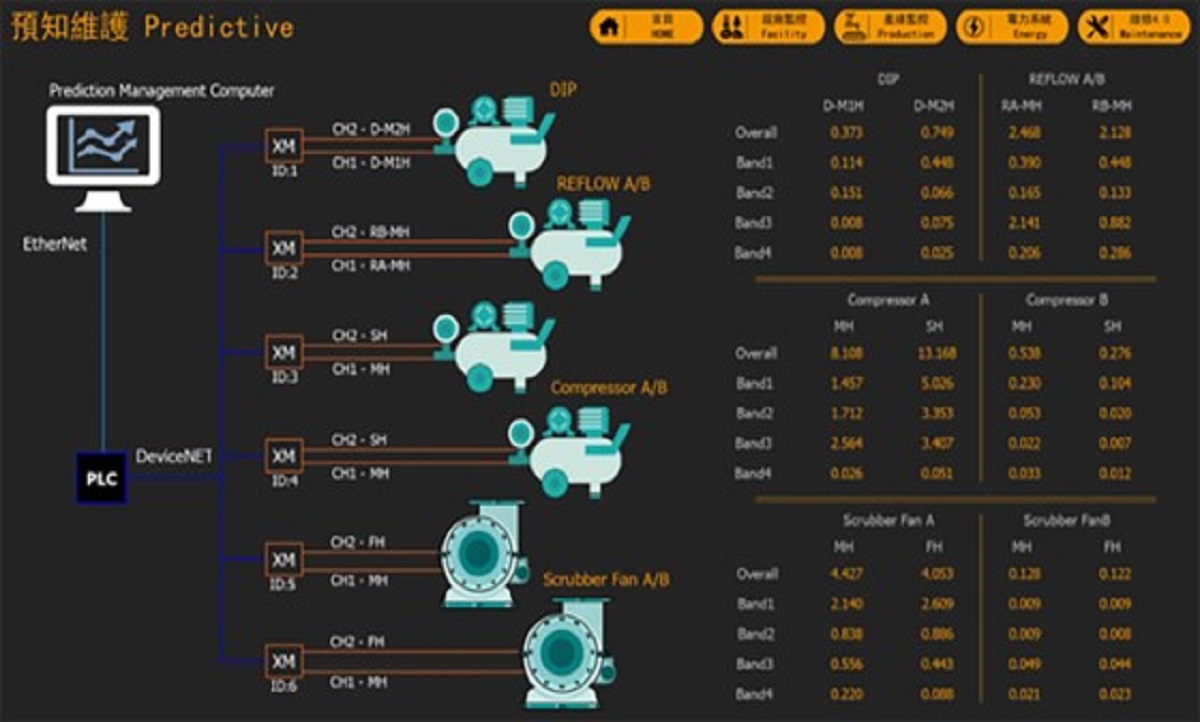
ERP/MES
With the iAT2000 system, revenue and shipment status of global subsidiaries are displayed on the dashboard, and data can be viewed in units of days, months, and years according to needs. The monthly data of each business group within the headquarter office can be reviewed through different pie charts, and the goods and unshipped data are presented in real-time dynamics.
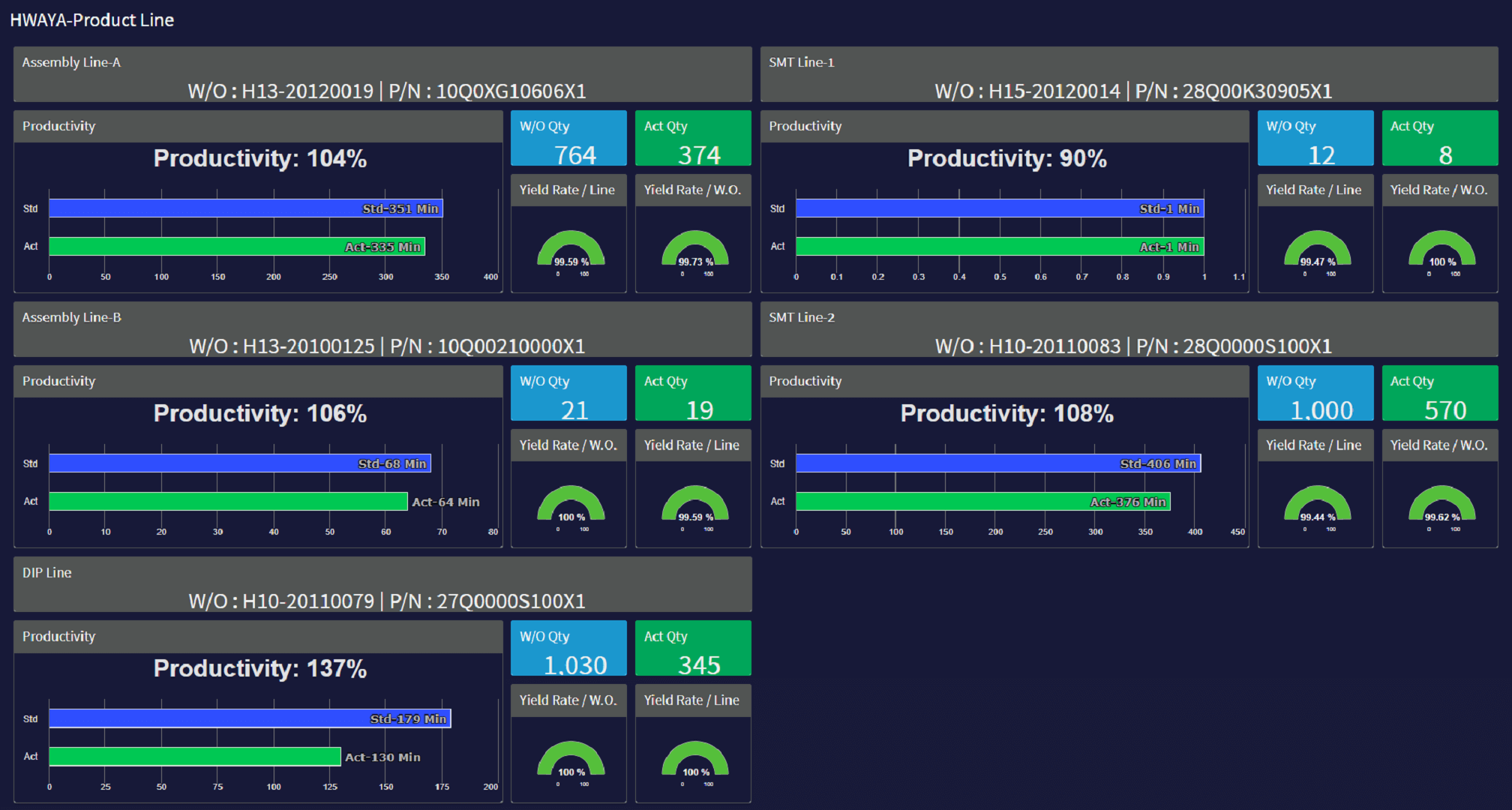
The estimated production capacity, target production capacity, and real-time production capacity are listed according to different production lines. Each production status is presented with a different curve and be combined to form a comprehension of the entire production is at full load, line change, or new product introduction.
Cybersecurity
NexAIoT’s information security technology is specialized in the Operational Technology (OT) layer that extends the protection layer of OT equipment from SCADA/HMI to the lowest level of the controller and I/O. The embedded monitoring system integrates security chips with Machine Learning to form the last line of defense to protect the security challenges of Industry 4.0, ranging from the cloud to the central office. The ICS security monitoring platform displays the security status of the SCADA host and automation control in real- time plus the monitoring of the entire control layer network flow and unknown IP location. The monitoring levels can be divided into ten levels, levels 1 to 6 are displayed as Safe in green, levels 7 and 8 are Warning in yellow, and levels 9 and 10 are Dangerous in red. The intuitive design allows managers to see the problem immediately and react in time.
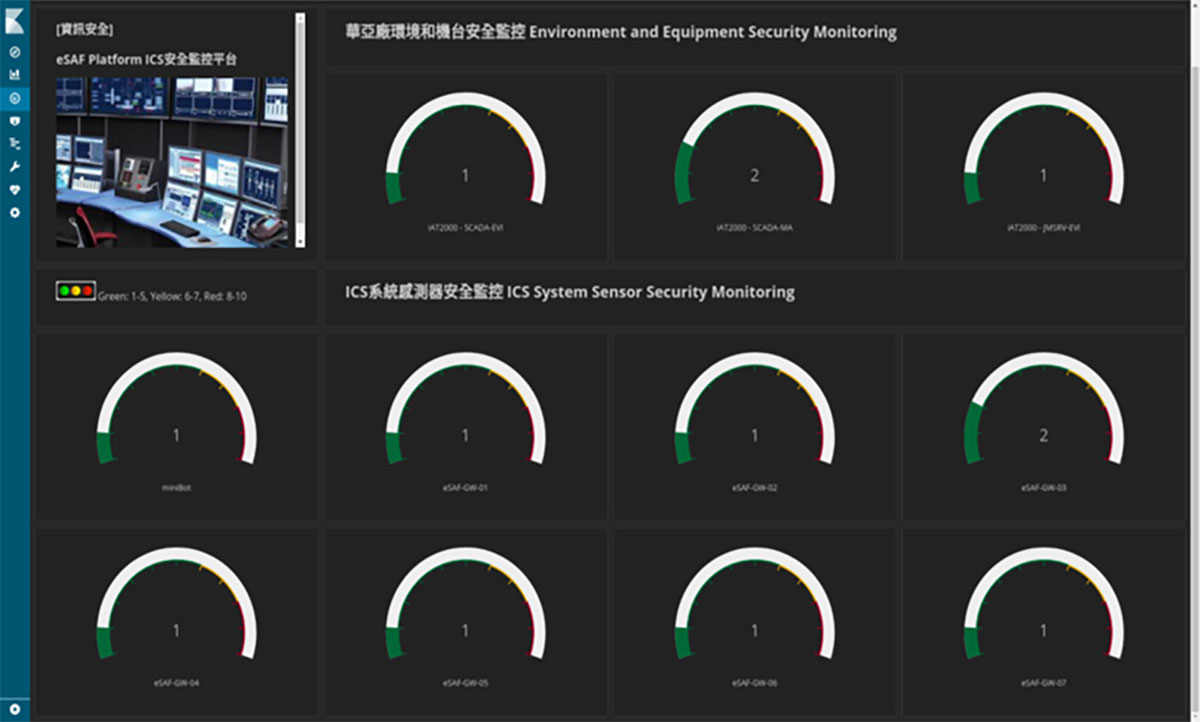
3D Factory
The actual factory environment is expanded into a 3D visualized factory building to achieve precise equipment monitoring with a sense of space. Augmented reality (AR) glasses are configured to share images through the camera on the glasses, allowing customers to provide remote guidance for security checks and maintenance.
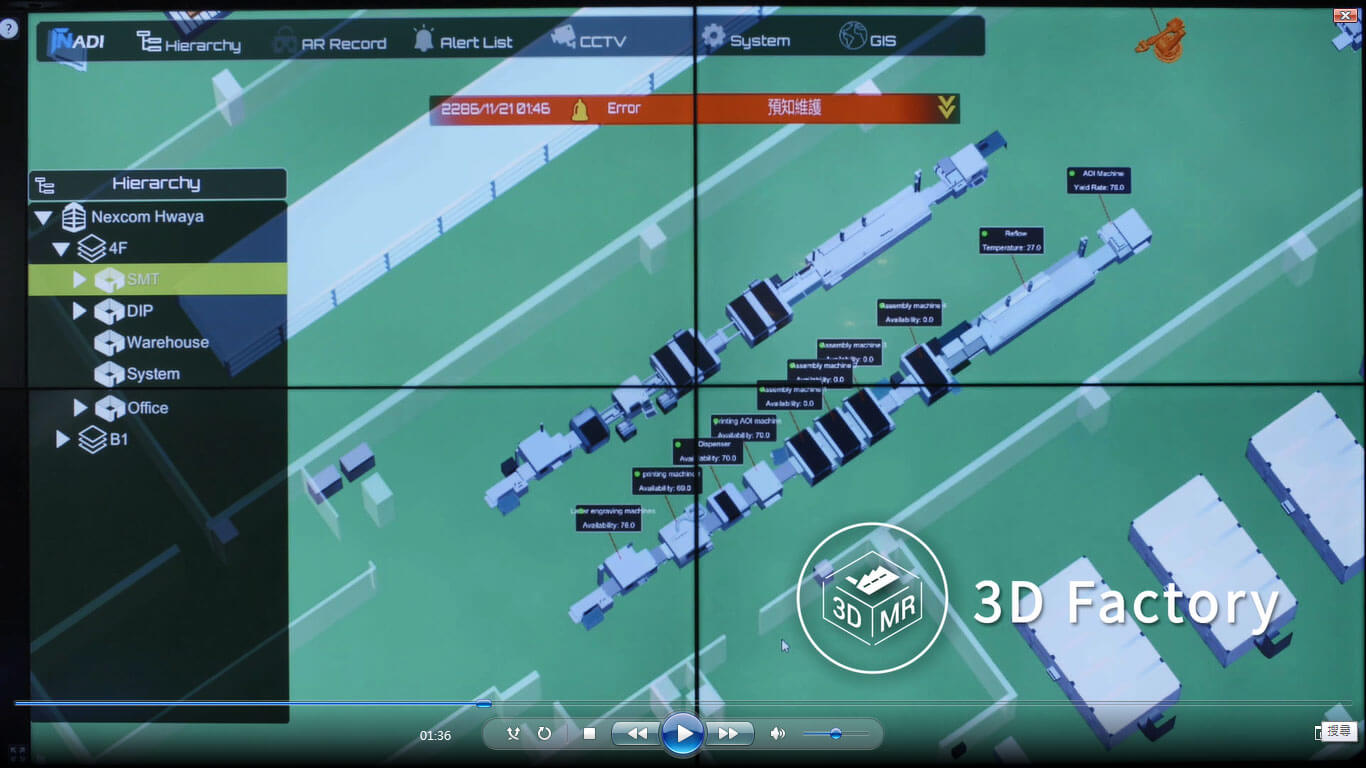
Mesh Wi-Fi
nCARE is aimed at meeting system administrators’ management needs with network equipment. The system is designed with network management and Modbus protocol. It manages not only NexAIoT products, but also third-party equipment. Better than other network management software, nCARE can directly control the device layer, and it has the functions below:
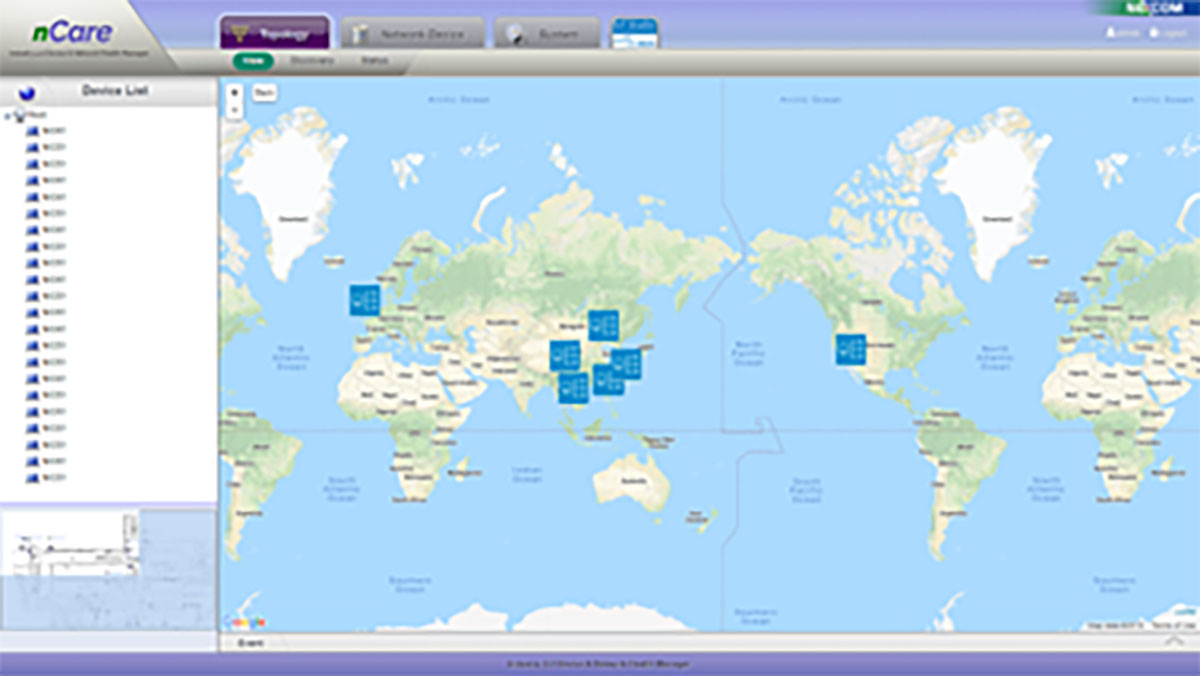
Operation
- Topology view and status update
- Traffic monitoring and alert
Security
- Topology view and status update
- Traffic monitoring and alert
Management
- Configuration backup and remote mapping upgrade
- IP conflict detection and alert
- Potential loop detection and alert
- App for mobility management
iPDM4.0
The Industry 4.0 real-time supervision of production costs uses the smallest "work order" unit as the cost and concurrently integrates the MES and ERP settlement systems to help companies grasp the actual cost of a single customer in time.
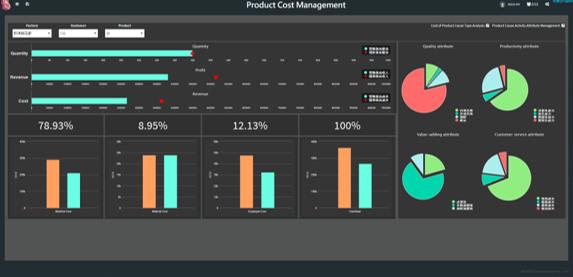
Customer Costs
Keep abreast of the customer's revenue, cost, and profit margin at any time. Alert orders that do not meet the pre-set standards and provide the basis for business departments to adjust quotations.
Work order cost
In touch with the accumulated cost of each work order at any time, assist on-site personnel in understanding the current cost of each work order in real-time, and reducing unnecessary time and cost investment.
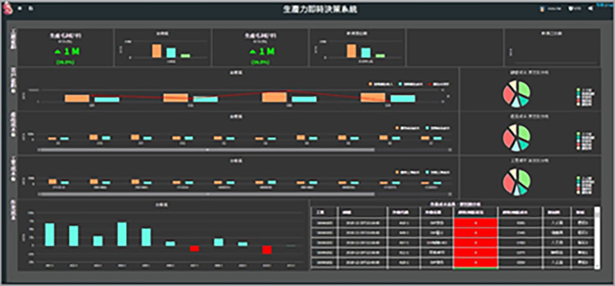
Product Cost
Up-to-date on the cost of each product and understand the difference between standard and actual costs.
Operation Time
Control the current operation progress of each work order at all times and assist on-site management personnel in comprehending possible problems and solving them quickly.